
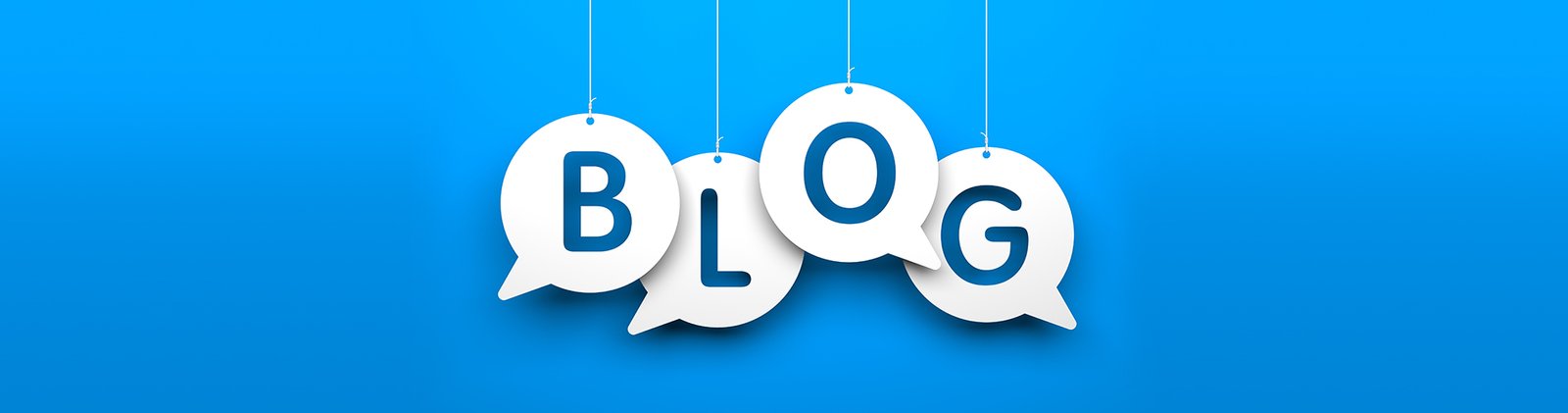
Producción de tapones de plástico: De la materia prima a los tapones de 28 mm
Tapones de botellas de plástico, más conocidos como tapones o cierres, desempeñan un papel crucial en el envasado cotidiano. Tanto si se coloca un tapón de 28 mm en una botella de agua como si se enrosca una tapa de 28 400 en un envase de zumo, estas diminutas piezas tienen una gran importancia para la protección del producto. Sin embargo, mucha gente no suele preguntarse cómo se fabrican estos tapones de plástico.
Esta guía se adentra en el viaje salvaje, desde los gránulos de resina en bruto hasta el elegante cierre flip top 28 410, listo para la acción.
Preparación de la materia prima: El comienzo olvidado
Antes de diseñar un Tapón de botella de agua de 28 mmTodo empieza con la resina. La mayoría de los tapones de botellas de plástico empiezan su vida como gránulos de polietileno (PE) o polipropileno (PP). Estos pequeños gránulos se secan a fondo porque la humedad estropea mucho el producto final.
Las fábricas que almacenan materias primas como los tapones de PET de 28 mm suelen vigilar la temperatura y la humedad como halcones. Sin este paso, los tapones de 28 410 nunca encajarían perfectamente en su bebida favorita.
Proceso de extrusión: Fusión y conformación
Una vez lista, la resina plástica pasa a la fase de extrusión. Imagínese una máquina gigante que tritura los gránulos y los funde en un flujo viscoso. La sustancia viscosa sale disparada a través de matrices que forman largos tubos de plástico.
Para cierres como tapa abatible 28mm o incluso tapa de disco superior 28 410, la calidad de la extrusión debe seguir siendo de primera. Si algo falla aquí, las dimensiones, como las medidas precisas de la tapa 28 400, podrían quedar muy lejos.
Moldeo por inyección: Magia en un instante
Después de la extrusión, las cosas se calientan de verdad, literalmente. En el moldeo por inyección comienza el verdadero arte. El plástico fundido entra en moldes cuidadosamente elaborados bajo una intensa presión. Un molde puede producir un Tapa abatible de 28 mm mientras otro bombea tapa flip top 28 estilos.
En cuestión de segundos, obtendrá una pieza perfectamente formada. Las marcas que buscan tapas plásticas de 28 mm cuentan con ciclos rápidos y formas nítidas. De lo contrario, los tapones de 28 mm defectuosos pueden causar estragos en las líneas de embotellado más adelante.
Refrigeración y control de calidad: No hay margen para el error
Recién moldeado tapones de plástico deben enfriarse rápidamente para mantener su forma. Los avanzados sistemas de refrigeración actúan de inmediato, congelando cada cresta y cada detalle del cierre a presión.
Los operarios examinan las muestras como halcones para detectar defectos a tiempo. Tanto si se comprueba un tampa disc top 28 410 como si se inspecciona un tapón ropp de 28 mm, la consistencia es fundamental. Las piezas deformadas no solo tienen mal aspecto, sino que pueden tener fugas, agrietarse o atascar la maquinaria.
Impresión y personalización: Hora de brillar
Una vez superada la prueba, Tapones de plástico hacia la personalización. Los propietarios de marcas pueden querer un logotipo, advertencias de seguridad o colores extravagantes en la superficie. Técnicas como la tampografía o los métodos digitales embellecen los tapones sencillos, convirtiendo una básica 28 410 abatible en un distintivo de marca.
Incluso las variantes de tapa de disco de 28 415 adquieren colores brillantes y acabados elegantes. Un tapón de plástico de 28 mm bien diseñado no solo cierra una botella, sino que se convierte en un arma de marketing.
Montaje y embalaje: Preparándose para el gran momento
Dependiendo del diseño, algunos cierres requieren un montaje adicional. Piense en los tapones de tirador 28 410: tienen piezas móviles que deben encajar a la perfección.
Las inspecciones finales detectan cualquier valor atípico antes del embalaje. Tapones de plástico como los modelos tampa flip top 28mm o 28 400 flip top cap se cuentan, se embolsan y se envían a las plantas de llenado. El embalaje debe proteger cada pieza del polvo, la estática o los golpes durante el trayecto.
La elección entre un tapón abatible de 28 410 o un tapón pco recto de 28 mm depende del uso final del cliente. Agua, aceite, zumo, champú... cada uno exige un ajuste perfecto.
Reflexiones finales: Por qué es importante para su empresa
Entender cómo los tapones de plástico de las botellas pasan de ser humildes gránulos a productos de aspecto afilado como tapa abatible 28mm ayuda a los compradores a tomar decisiones más inteligentes. Tanto si se trata de comprar tapones 28 410 como tapones de 28 mm para una nueva línea de productos, conocer los pasos a seguir aporta poder.
Los fabricantes que controlan cada fase consiguen un mejor rendimiento del tapón 28 410. Desde la selección de materiales resistentes hasta el clavado de las dimensiones de la tapa 28 400, cada movimiento cuenta.
Un aprovisionamiento inteligente de cierres como los tapones de PET de 28 mm o las variedades de tapones de botella de 28 mm se traduce en menos quebraderos de cabeza a posteriori. Los tapones de plástico de calidad superior mantienen los productos frescos durante más tiempo, protegen su imagen de marca e incluso aumentan la confianza del consumidor sin que usted mueva un dedo.