
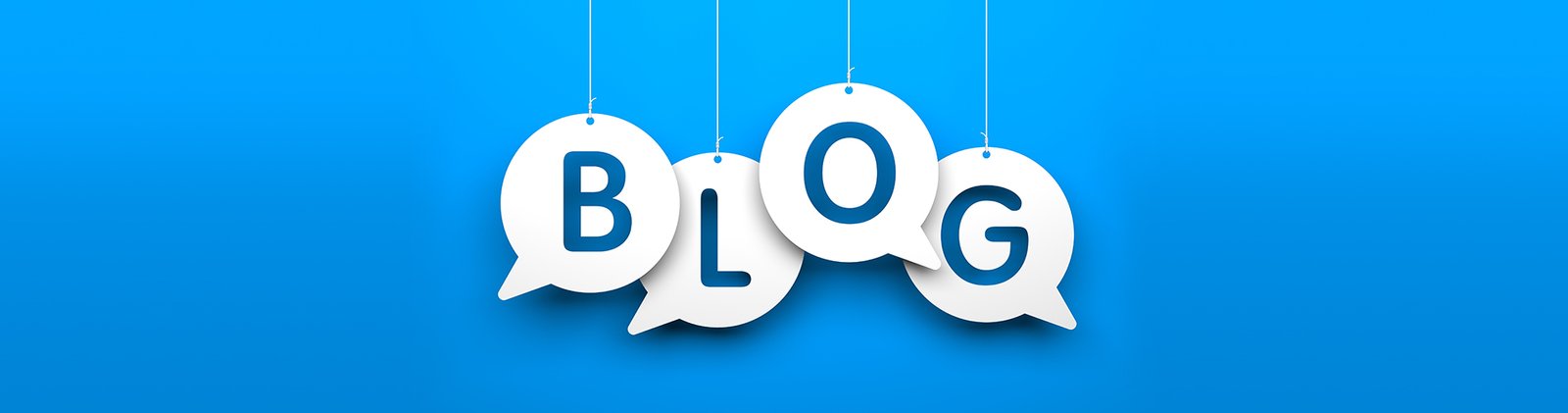
크로스 슬릿 밸브의 작동 원리: 현대적인 요구 사항을 위한 솔루션
크로스 슬릿 밸브-유체 제어의 작은 영웅인 이 부품은 액체가 한 방향으로 흐르도록 유지하면서 역류를 차단합니다. 물병부터 의료 기기까지 모든 제품에 사용되는 이 부품은 단순함과 신뢰성을 겸비하고 있습니다. 일반적인 고객 고충을 해결하면서 이러한 부품의 메커니즘, 과제 및 최상의 용도를 분석해 보겠습니다.
B. 안전 및 무결성
소재의 품질이 중요합니다. 식품 등급 실리콘은 물병 체크 밸브에 필수적인 오염을 방지합니다. 의료용 옵션은 멸균 처리가 가능합니다. 씰이 불량하면 누수 또는 제품 변질의 위험이 있으므로 내화학성 및 내구성 테스트를 거친 밸브를 선택하세요.
C. 준수해야 할 규칙
규정은 다양합니다. 식품 접촉 밸브는 FDA 승인이 필요합니다. 의료 기기는 ISO 인증이 필요합니다. 항상 해당 산업에 맞는 표준을 확인해야 합니다. 규정 준수를 건너뛰면 리콜이나 안전 위험이 발생할 수 있습니다.
II. 일반적인 장애물
A. 재료 매치업
모든 실리콘이 모든 곳에서 작동하는 것은 아닙니다. 가혹한 화학 물질은 표준 밸브를 저하시킵니다. 고온은 저렴한 소재를 휘게 합니다. 연료용 과산화물 경화 실리콘과 같은 특수 혼합물을 선택하면 이 문제를 해결할 수 있습니다.
B. 프로덕션 골칫거리
정밀 절삭 슬릿 개구부에는 고급 성형이 필요합니다. 사소한 오차도 유량 불일치의 원인이 됩니다. 마이크로 덕빌 밸브 생산에 경험이 풍부한 제조업체와 협력하십시오. 자동화된 조립 라인은 결함을 줄여줍니다.
C. 예산 대 친환경 목표
고품질 실리콘은 저렴하지 않습니다. 하지만 비용을 절감하면 교체가 잦아집니다. 밸브 크기를 최적화하거나 폐 실리콘을 재활용하여 비용 균형을 맞추세요. 환경을 생각하는 브랜드는 이제 재활용 가능한 밸브 설계를 선호합니다.
최종 테이크
크로스 슬릿 밸브 산업 전반의 유량 제어 문제를 해결합니다. 스포츠 물병을 만들든 의료용 디스펜서를 만들든 올바른 실리콘 슬릿 밸브를 선택하는 것은 요구 사항, 재료 및 트렌드를 이해하는 데 달려 있습니다. 혁신과 신뢰성을 우선시하는 공급업체와 협력하여 앞서 나가세요.
크로스 슬릿 밸브 에는 4개의 첨두 개구부와 구불구불하지 않은 직선형 흐름 경로가 있습니다. 따라서 기기와 물질을 모두 밸브를 통해 안내하거나 밀어 넣을 수 있습니다. 크로스 슬릿 밸브 은 최소 침습 수술의 트로카 및 지혈 포트에 자주 사용됩니다. 크로스 슬릿 밸브는 백업 씰과 함께 의료 기기와 함께 삽입된 절개 부위나 체강에서 체액이나 가스가 누출되는 것을 방지합니다. 크로스 슬릿 밸브의 4개의 커스피드는 제거 단계에서도 누출을 방지합니다. 슈푸캡의 특허받은 액세스 밸브는 더 큰 직경과 압력 범위에 맞게 사용자 지정할 수 있는 고유한 디자인을 제공합니다.