
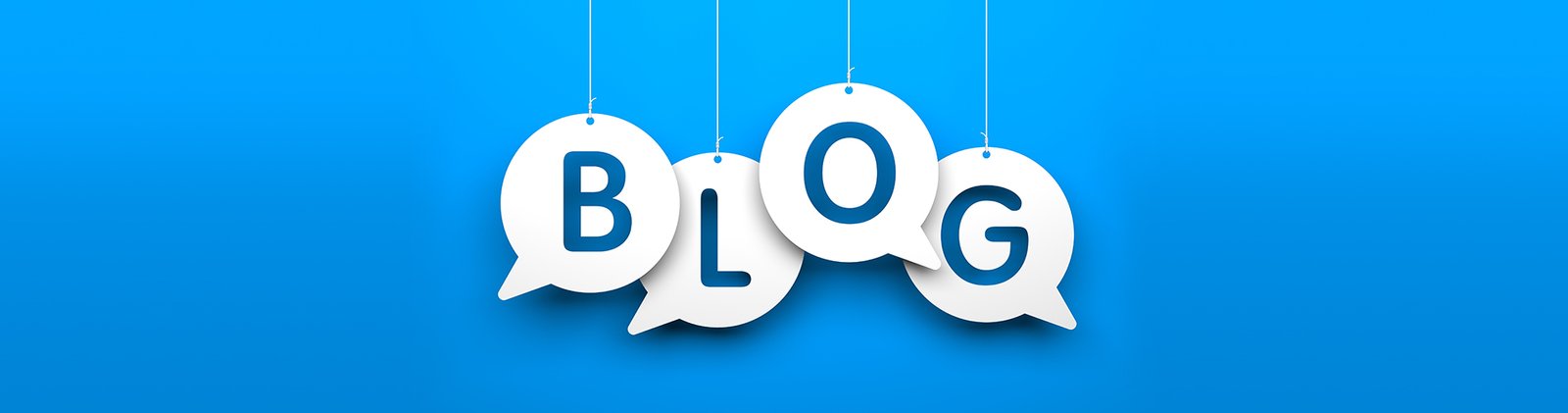
플립 탑 병 뚜껑 금형 구조를 선택하는 방법은 무엇입니까?
Selecting the right mould structure for 플립 탑 병뚜껑 can feel tricky. Whether you’re producing 플립 탑 캡 플라스틱 병 for shampoo, shower gel, or food jars, the structure behind the cap truly matters. It’s not just about the look. Performance, durability, and cost all ride on your mould design.
But first, let’s make sure we’re on the same page. A flip-top cap refers to a hinged plastic cap that can be flipped open with a finger, while the main body remains attached to the container. Common on bottles for personal care, kitchen condiments, or pharmaceuticals, these caps offer that one-hand ease consumers love.
Whether you’re after a 중국 토마토 병 플립 탑 캡 또는 din 18 flip top cap, picking the proper mould structure will affect your production yield, cap closure quality, and downstream packaging compatibility.
1. Flip Top Cap Appearance – It’s Not All About Looks
Sure, a 플립 탑 캡 20/410 또는 플립 탑 캡 28/410 needs to look clean and presentable. But appearances do more than attract eyeballs. The outer shell should match your bottle’s shape—maybe you’re working with a cylinder bottle flip top cap or something more curved. Either way, the mould has to deliver a cap with smooth finishes and precise dimensions.
Customers won’t tolerate rough edges or inconsistent hinge movement. That’s why polishing and venting in the mould must be tuned carefully. Poor design? Say hello to leakage, misalignment, or brittle hinges.
2. flip top bottle caps Structure – Hinge Matters More Than You Think
Every flip-top hinge type brings a bag of pros and cons. Here’s where things split into three main paths:
External hinge design – Basic, cheap, and usually less durable. Works well for caps used infrequently or on larger flip top gas cap adapter 스타일.
Living hinge design – One-piece solution with a flexible plastic bridge. Used in most modern 플립 탑 캡 and closures. Requires precise injection conditions and uniform wall thickness.
Double injection hinge – More expensive but adds color and texture options. Useful when aesthetic rules or premium branding is the goal. You’ll often see this in high-end 디스크 탑 플립 캡 packaging.
Your choice? Depends on product type, closure force, and whether the cap must survive repeated opening.
3. Flip Top Bottle Caps Raw Materials – Plastic Ain’t Just Plastic
You wouldn’t build a car from cardboard. Likewise, you don’t make high-quality crest flip top cap styles with cheap poly. Polypropylene (PP) is a common choice thanks to its flexibility and food-safe profile. But don’t skip checking the melting point and chemical resistance either. Certain shampoos, for example, require a higher-grade resin than ketchup bottles.
And yes, material shrinkage affects the final dimensions. That means your mould needs to account for that too.
Think About the Machinery Too
Even the best mould won’t help if your flip top cap closing machine jams every 50 units. The mould and machine must talk to each other. If the cap has a deep snap-on groove or a tight seal, then your machine needs enough torque and precision to press it in place without cracking anything.
Ask your supplier to provide a flip top cap drawing showing the exact geometry. Cross-check this with the machine’s performance specs. No guesswork allowed.
Balancing Cost, Speed, and Output
High-cavity moulds crank out more caps per cycle but cost more upfront. Low-cavity ones are cheaper to build yet slow you down long term. So if you’re scaling fast in the 플립 탑 디스펜서 캡 시장, don’t cheap out too soon. A better investment now might save you pain later.
Also, keep in mind changeovers. Modular mould designs help switch sizes or cap types quicker. Especially if you juggle multiple lines—say both 플립 탑 캡 20/410 그리고 플립 탑 캡 28/410.
Wrapping Up Without Sugarcoating It
Choosing a flip top bottle caps mould structure isn’t just a checkbox. It plays into your entire packaging line. It decides how your product looks, feels, and behaves in consumers’ hands. Get it wrong and you’re stuck with returns or worse—angry reviews.
Study your hinge options. Match materials to the liquids. Align your tooling with your machines. Whether you’re chasing low-cost output or fancy finishes, there’s no one-size-fits-all answer here.
But with sharp planning and a close eye on details, you can absolutely land a mould setup that delivers sturdy, stylish 플립 탑 캡 및 클로저—ones that click, seal, and pour with confidence.