
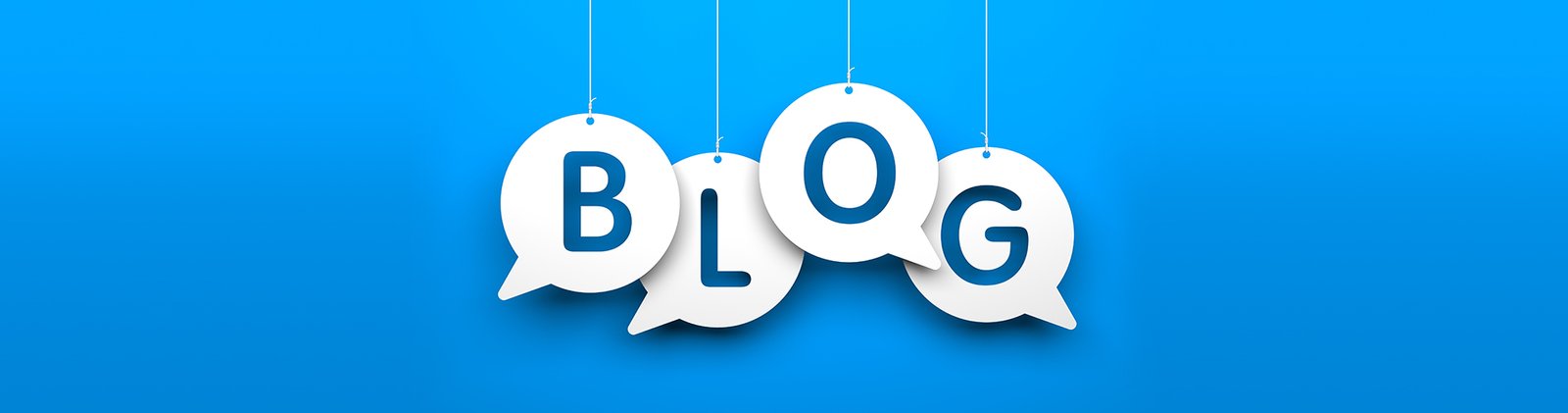
병 제조에서 플립 탑 뚜껑 사용 최적화하기: 더 나은 결과를 위한 실용적인 가이드
병 생산에서는 소박한 플립 탑 뚜껑까지 모든 디테일이 중요합니다. 개인 위생용품, 가정용 액체, 치약 튜브 등 어떤 용도로 사용하든 올바른 핏과 기능을 갖추려면 플립형 플라스틱 캡 는 단순한 외관 이상의 영향을 미칠 수 있습니다. 설계 결함, 금형 품질 또는 공급 불일치로 인해 공정이 지연되거나 제품 손실이 발생할 경우 제조업체와 구매자는 모두 골치 아픈 문제에 직면하게 됩니다. 그렇다면 이러한 문제를 어떻게 해결할 수 있을까요? 플라스틱 병 플립 탑 캡 문제가 있나요?
이 가이드에서는 플립형 뚜껑으로 작업할 때 효율성, 안정성, 비용 효율성을 높이는 방법에 대해 자세히 설명합니다. 뚜껑의 기능 이해부터 스마트한 기술 변화를 알아보는 방법까지, 빠르게 변화하는 시장에서 필요한 모든 것을 설명합니다.
플립 탑 뚜껑 기능 및 활용에 대한 이해
플립형 뚜껑은 단순한 뚜껑 그 이상입니다. 편리함을 제공하고 위생을 개선하며 흘림을 줄여줍니다. 이러한 뚜껑은 샴푸병, 치약 튜브, 물병, 청소용품 등에서 흔히 볼 수 있습니다. 사용이 간편하기 때문에 특히 사용량이 많은 가정과 이동이 잦은 라이프스타일에서 선호도가 높습니다.
다음과 같은 제품 플립형 치약 뚜껑 또는 플립 탑 스크류 캡 실용적인 역할을 합니다. 적당한 양을 추출하고 노즐을 깨끗하게 유지하는 데 도움이 됩니다. 일부 스타일은 치약 튜브용 플립 탑 캡-또한 많은 구매자에게 중요한 어린이 친화적인 제품입니다.
여러 가지 형식이 존재합니다. 다음과 같은 형식이 있습니다. 플립형 물병 뚜껑, 플립형 디스펜서 캡및 다음과 같은 특수 유형 라이프팩토리 플립 탑 캡 교체 부품. 제품의 목적에 맞는 형식을 파악하는 것은 추가 비용 없이 우수한 기능을 구현하는 데 있어 핵심입니다.
제조업체와 구매자가 직면하는 일반적인 과제
플립 탑 캡의 인기에도 불구하고 품질이 떨어지면 문제가 발생합니다. 가장 널리 퍼진 문제 중 하나는 금형 품질 저하입니다. 열등한 플립 탑 캡 몰드 디자인은 파손, 누수 또는 마개가 잘못 정렬될 수 있습니다. 병이 진열대에 오르기도 전에 돈을 낭비하는 셈이죠.
공급이 일정하지 않으면 생산 라인도 엉망이 됩니다. 만약 플립 탑 캡 공급업체 안정적으로 배송하지 못하면 일정이 지연되어 고객에게 손해를 끼칠 위험이 있습니다. 구매자는 종종 약한 경첩이나 느슨한 씰에 대해 불만을 토로합니다. 플립 탑 캡 제조업체.
또 다른 문제는? 호환성입니다. 일부 플립형 플라스틱 캡 특히 맞춤형 병과 함께 사용할 때는 충분히 꽉 조이지 마세요. 여기에 맞지 않으면 배송 또는 보관 중에 누출이 발생할 수 있습니다.
플립 탑 뚜껑 사용 최적화를 위한 모범 사례
이제 혼란을 해결하는 방법에 대해 이야기해 보겠습니다. 올바른 조치가 큰 차이를 만듭니다.
먼저 고급 금형에 투자하세요. 신뢰할 수 있는 플립 탑 캡 몰드 는 결함이 적은 일관된 부품을 수천 개 생산할 수 있습니다. 다음을 전문으로 하는 제조업체를 살펴볼 가치가 있습니다. 플립형 플라스틱 병뚜껑 를 사용하여 고정밀 결과를 얻을 수 있습니다.
둘째, 호환성을 조기에 테스트하세요. 프로덕션이 시작될 때까지 기다리지 마세요. 선택한 플립형 플라스틱 캡 를 미리 병에 부착하세요. 이를 통해 대규모 반품으로 이어질 수 있는 디자인 불일치를 사전에 파악할 수 있습니다.
품질 관리 체크리스트를 사용하세요. 토크, 힌지 강도, 씰 무결성을 평가합니다. 이렇게 하면 약한 마개가 몰래 통과하는 것을 방지할 수 있습니다. 치약과 같은 스퀴즈 제품의 경우, 팀은 다음을 검사해야 합니다. 플립형 치약 뚜껑 조기 마모를 잡아야 한다는 압박을 받고 있습니다.
마지막으로, 안정적으로 작업하세요. 플립 탑 캡 공급업체 일괄 추적 및 정시 배송을 제공합니다. 배송 지연 또는 저품질로 인한 라인 중단의 위험을 줄일 수 있습니다.
플립 탑 뚜껑 디자인의 미래 기술과 트렌드
상황이 빠르게 변화하고 있습니다. 이제 지속 가능성은 다음과 같은 방식으로 변화를 주도하고 있습니다. 플립탑 캡 만들어집니다. 재활용 가능한 소재, 생분해성 플라스틱, 부품 수가 적은 캡의 인기가 높아지고 있습니다. 특히 다음과 같은 경우에 해당됩니다. 플립 탑 스크류 캡 식품 등급 포장에 사용되는 유형입니다.
3D 프린팅도 그 역할을 하기 시작합니다. 대량 생산 전에 더 빠르게 금형을 테스트하고 더 빠르게 조정할 수 있습니다. 따라서 새로운 제품을 설계할 때 시간을 절약하고 낭비를 줄일 수 있습니다. 플라스틱 병 플립 탑 캡 모양.
스마트 캡도 등장하고 있습니다. 몇몇 개발자는 다음과 같은 버전을 테스트하고 있습니다. 플립형 물병 뚜껑 수분을 추적하거나 조작을 감지할 수 있습니다. 지금은 다소 생소할 수 있지만 흥미로운 미래를 예고하는 기술입니다.
또 다른 성장 추세는? 맞춤형 컬러 매칭과 텍스처링으로 새로운 병 디자인에 많은 비용을 들이지 않고도 브랜드를 돋보이게 할 수 있습니다. 간단한 업데이트로 오래된 제품을 리뉴얼하고자 하는 기업에게 큰 도움이 됩니다.
결국 병 제조의 성공은 작은 것 하나하나를 제대로 처리하는 데 달려 있습니다. 플립 탑 뚜껑은 사소해 보이지만 고객 만족도를 좌우할 수 있습니다. 숙련된 플립 탑 캡 제조업체 올바른 재료, 견고한 성형 공정, 스마트 물류를 통해 골칫거리를 대폭 줄일 수 있습니다.
따라서 라이프팩토리 플립 탑 캡 포장 또는 새로운 라인 출시 플립형 디스펜서 캡이러한 사소한 세부 사항에 주의를 기울이면 한발 앞서 나가고 문제를 피할 수 있습니다.
더 원활한 운영과 더 나은 결과를 얻으려면 안주하지 마세요. 테스트하고, 조정하고, 적합한 파트너를 선택하세요. 병 생산에는 "그냥 뚜껑"이라는 것은 존재하지 않기 때문입니다.