
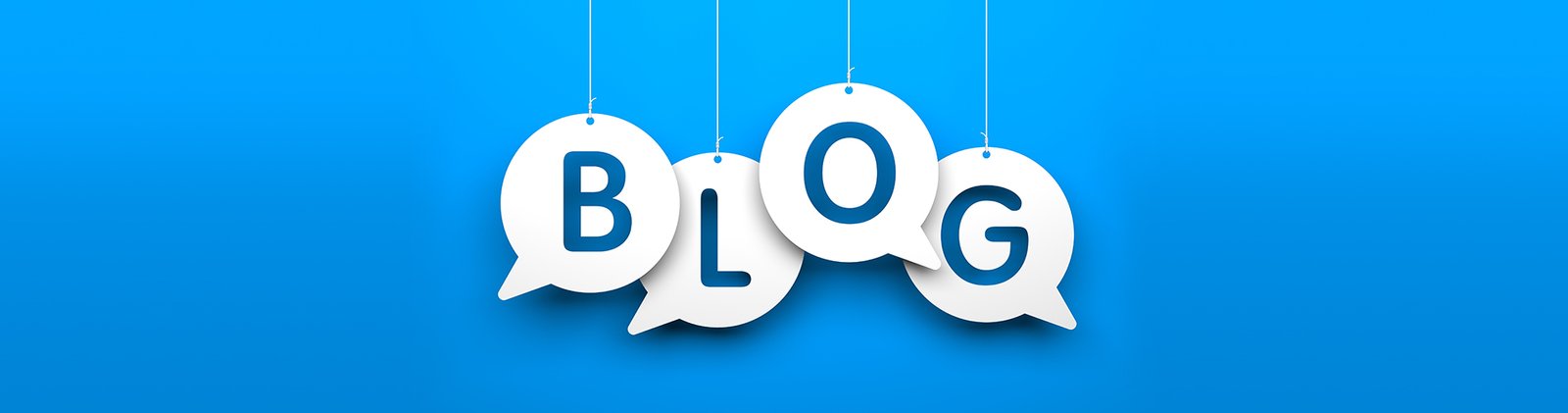
Kaip sukurti sandarų sportinio butelio dangtelį: Inžinieriaus įžvalgos
Creating a truly leak-proof cap for sports bottles isn’t just a manufacturing challenge—it’s a real-life problem for users who deal with spills during workouts, hikes, or travel. This guide unpacks the engineering strategies behind the perfect leak-proof cap, especially those based on apverčiamas dangtelis technologies such as Apverčiamasis dangtelis 20/410, 24/410, ir 28/410. We’ll also explore how elements like silikoniniai vožtuvai, hinge design, and the right apverčiamo dangtelio pelėsis can make or break a design.
Why a Leak-Proof Cap Matters More Than You Think
Nobody likes water dripping down their gym bag or soaking their papers. A leak-proof cap solves that nightmare. For athletes and commuters alike, sealing reliability ranks above aesthetics. Apverčiamieji dangteliai, especially with precision hinges and tight molds, offer a solid starting point—but they need careful design work.
Flip Top Cap Design Begins with Material Choice
Engineers usually lean on polypropylene or HDPE for the plastikiniai buteliai su apverčiamu dangteliu market. But plastic alone won’t seal a bottle. The inner workings, such as a apverčiamas dangtelis su silikoniniu vožtuvu, do the heavy lifting. Silicone creates a flexible, tight seal that adapts to pressure without cracking or degrading over time.
Fit Matters: Choose the Right Neck Size—20/410, 24/410, or 28/410
A Apverčiamasis dangtelis 20/410 fits a narrow bottle neck. A flip top cap 24/410 is your go-to for medium profiles. Apverčiamasis dangtelis 28/410 fits beefier bottles. Mismatched sizes lead to poor seals. Worse, they leak under pressure or movement. A leak-proof design starts with a snug match between cap and bottle neck.
Flip Top Cap Hinge Design: The Hidden Hero
The hinge on a apverčiamas dangtelis does more than just open and shut. It dictates how easily the user can seal the bottle one-handed. But more importantly, it affects the tension that holds the cap closed. A weak hinge? That’s a dribbler waiting to happen.
A tight, yet flexible apverčiamo dangtelio lanksto konstrukcija keeps the lid flush against the valve. Engineers often tweak the thickness of the living hinge or reinforce it with ribs to extend lifespan and resist fatigue.
Use 3D Prototypes: Flip Top Cap 3D Model for Pre-Testing
Before committing to expensive tooling, engineers simulate everything with a flip top cap 3D model. With the right model, you can test stress points, hinge behavior, valve compression, and sealing pressure. Mistakes found here are cheaper than later on the production floor.
Advanced Leak Prevention: Silicone Valves and Double Seals
Adding a apverčiamas dangtelis su silikoniniu vožtuvu changes the game. These valves flex slightly to release liquid during squeeze or sip, but remain tight under normal conditions. Combine that with a double-seal ridge inside the cap, and you’ve got yourself a lockdown seal.
These systems especially thrive in bottles designed for smoothies, protein shakes, or carbonated water. Pressure management matters more than most people think.
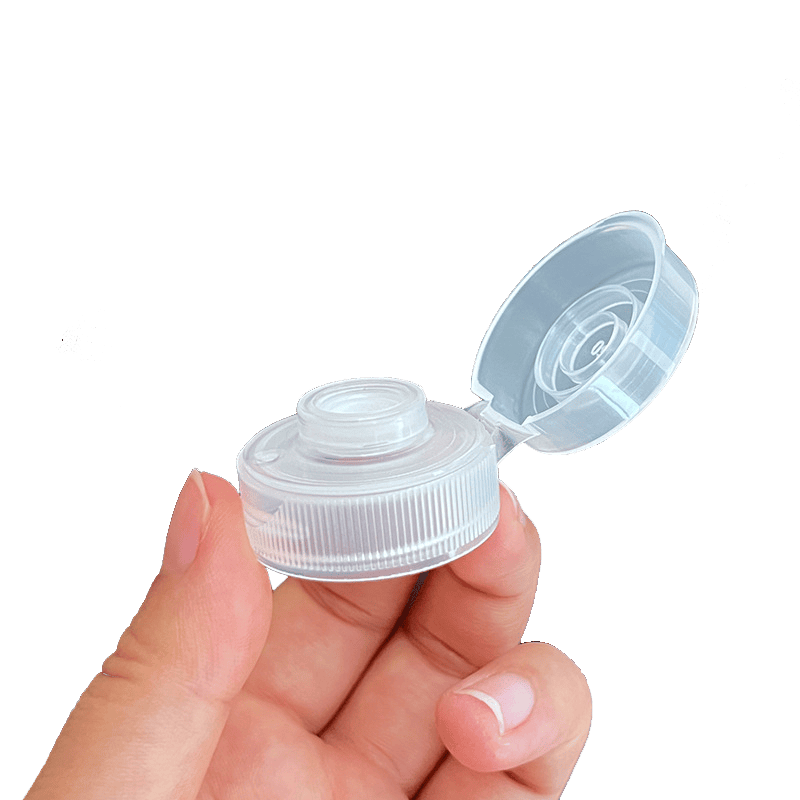
Gaukite konkurencingą
kraštas
Prekės ženklais pasitiki daugiau nei 20 šalių. Konkurencingos kainos, puikus aptarnavimas, individualus palaikymas.
From Mold to Mass Production: Flip Top Cap Mold Essentials
The design of your apverčiamo dangtelio pelėsis arba apverčiamo dangtelio formos dizainas shapes the final quality. Misalignments, shrinkage issues, or poor flow design create caps that won’t align or seal. Precision is king here.
Use multi-cavity molds for higher consistency
Include venting to prevent trapped air
Allow slight draft angles for easy demolding
A bad mold leads to warped caps. Warped caps leak. Don’t skimp here.
Flip Top Cap Closing Machine: Automation That Counts
After injection molding, caps get assembled and snapped onto bottles using a flip top cap closing machine. This machine must press with even force to avoid cap distortion. Misalignment? That crushes your seal, introducing tiny leaks no one sees until the bottle ends up upside-down in someone’s gym locker.
Machines must also align the hinge and valve perfectly. Human error at this stage ruins the whole batch.
Flip Top Dispensing Cap Market Trends and Demands
Svetainė Dozavimo dangtelių su atlenkiamu dangteliu rinka grows fast. Consumers demand convenience, but not at the cost of leaks. Eco-packaging also shifts the industry toward minimalistic but functional designs, including recyclable apverčiamieji dangteliai ir uždarymo įtaisai. More brands now request designs with swappable silicone inserts or replaceable seals.
Smart brands work with manufacturers who offer CAD access to the flip top cap 3D model and quick turnaround for prototype tooling.
Testing a Leak-Proof Cap—Don’t Just Shake It
Shake tests alone don’t tell the full story. Engineers use:
Pressure chamber tests
Inverted leak simulations
Drop tests from 1.5 meters
Long-term seal retention under stress
Leak-proof isn’t just about today—it’s about staying sealed next month too.
Conclusion: What It Takes to Design the Ideal Leak-Proof Cap
A leak-proof cap isn’t magic. It’s smart engineering. Use the correct flip top cap 24/410 arba 28/410 fit. Add a silikoninis vožtuvas for flexibility and pressure control. Choose a hinge that won’t quit. Test it early using a 3D model. Make sure the cap mold is flawless, and don’t cheap out on assembly with a low-grade closing machine.
Get all these right, and customers will never think about your cap again—which is exactly how it should be.
Ką sako mūsų klientai
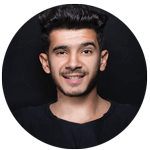
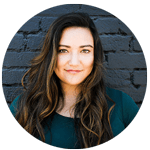
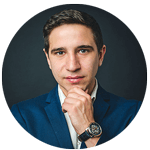
Quick Recap: Engineering Priorities for Leak-Proof Caps
Match neck sizes precisely (20/410, 24/410, 28/410)
Use food-grade silicone valves for adaptable seals
Design reliable hinges to maintain tension
Prototype early with 3D models
Invest in precise molds and assembly machinery
Test real-world performance, not just theoretical pressure
Atsakymų: 1